The reason why the
industrial chiller does not cool may be due to insufficient refrigerant, dirt in the condenser, improper position of the slide valve, leakage of cold air, fouling of the evaporator, and so on. The high-pressure alarm failure may be caused by frequent start and stop of the chiller, dirty pipeline, low or unopened cooling water flow, too much cold coal, poor heat dissipation of the condenser, and excessive opening of the expansion valve. The low pressure alarm failure may be due to insufficient refrigerant, excessive water volume or fouling of the condenser, leakage of the suction and exhaust valves, frosting of the evaporator, dirty filter of the evaporator, etc. Solving these faults requires implementing corresponding solutions, such as replenishing refrigerant, cleaning the condenser, adjusting the slide valve, cleaning or replacing the filter, and so on.

1.Insufficient cooling capacity: Lack of refrigerant
Industrial chillers, that is, during the operation of the unit, the liquid refrigerant flowing through the evaporator continuously absorbs heat in the water and begins to evaporate, and then becomes a low-temperature and low-pressure refrigerant after being compressed by the compressor and intercepted by the expansion valve. Therefore, if the chiller lacks refrigerant, it will inevitably affect heat absorption, resulting in low cooling efficiency. Insufficient refrigerant can be observed through the low-pressure gauge. For example, for a 5HP air-cooled chiller, the pointer of the low-pressure gauge should point to a value of 3.5-4.0. If the pointer is lower than this as shown in the figure below, it is obvious that the refrigerant is insufficient. The solution is to add refrigerant.
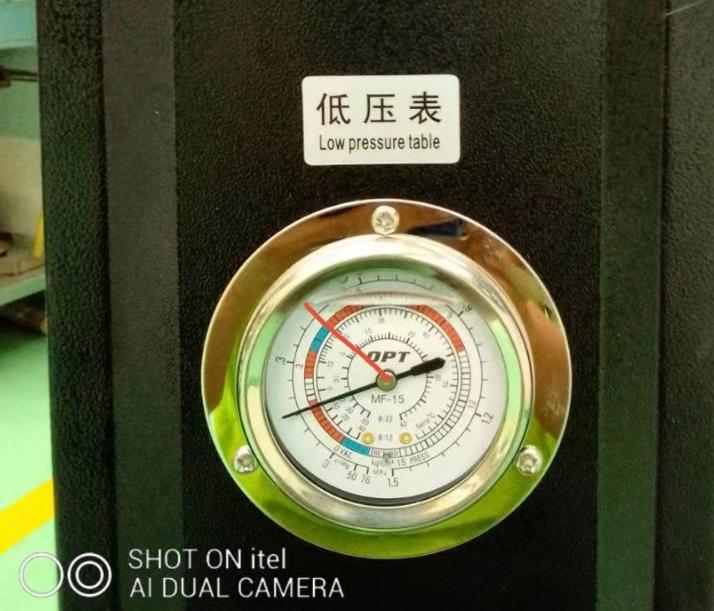
2.Dirt in the condenser: As one of the four major parts of the chiller, the condenser is a key component directly involved in refrigeration. The cooling water used by the chiller contains magnesium ions, calcium and 30 carbonates, which will form rust and scale, and the generation of rust will directly lead to poor heat exchange effect of the condenser, and the serious structure will block the pipeline, deepening the heat exchange effect. The solution is to check, descale and maintain the condenser.
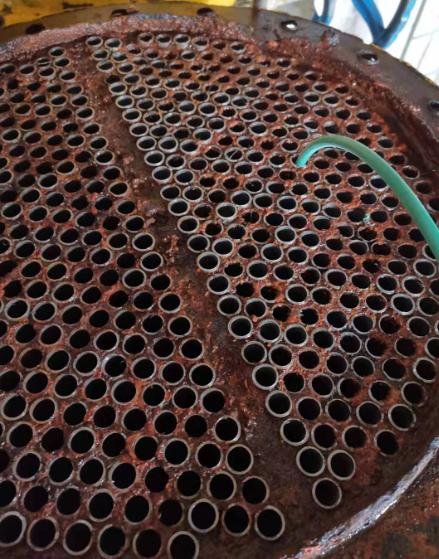
3.Reasons such as inappropriate slide valve position or component wear: Improper slide valve position, clogged suction filter, wear and tear of mechanical parts, cold air leakage, evaporator structure, insufficient fuel injection and other reasons will cause insufficient cooling capacity, which may cause the chiller to not cool.
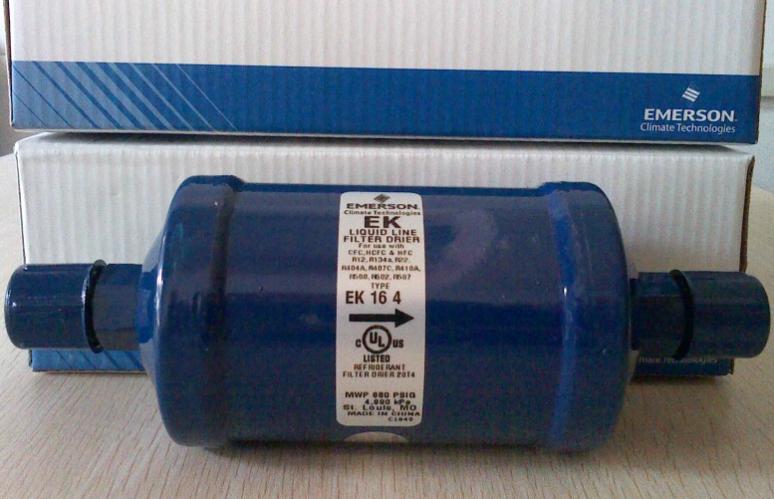
Solving the above-mentioned refrigeration failures of
industrial chillers requires: replenishing refrigerant, inspecting the condenser, descaling, maintenance, adjusting the slide valve, cleaning or replacing the filter, and maintenance of the rotor and bearing wear. Insufficient fuel injection, find out the cause and add oil, open the suction stop valve, find the leakage point of the refrigerator, check, descale and maintain the evaporator.
4. It may also be the cause of high-voltage alarm failure or low-voltage alarm failure;
Solution: A detailed solution article has been posted earlier.
4.Other reasons: Other reasons include evaporator structure, electrical system failure and so on. Solutions need to be case-specific.

In short, when using industrial chillers, it is necessary to carry out regular inspection and maintenance on the equipment, and to find and solve problems in time to ensure the normal operation of the equipment and long-term use of chillers. Understand, analyze and take appropriate solutions. If you cannot solve the problem by yourself, it is best to ask a professional technician to assist you.